引用本文: | 刘雨薇,李淳,冯世钊,王叶,周述军,靳爽.长寿命热障涂层失效机制、材料选择及结构设计研究进展[J].中国表面工程,2024,37(5):220~237 |
| LIU Yuwei,LI Chun,FENG Shizhao,WANG Ye,ZHOU Shujun,JIN Shuang.Research Progress on Failure Mechanism, Material Selection and Structural Design of Long-life Thermal Barrier Coatings[J].China Surface Engineering,2024,37(5):220~237 |
|
|
|
本文已被:浏览 699次 下载 434次 |
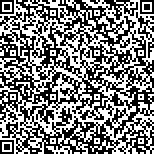 码上扫一扫! |
|
长寿命热障涂层失效机制、材料选择及结构设计研究进展 |
刘雨薇1,李淳1,冯世钊1,王叶2,周述军1,靳爽3
|
1.中国矿业大学(北京)机械与电气工程学院 北京 100083 ;2.中国北方车辆研究所 北京 100072 ;3.北京理工大学机械与车辆学院 北京 100081
|
|
摘要: |
热障涂层(Thermal barrier coatings, TBCs)是一种应用于航空发动机、地面燃气轮机等动力装备的高效功能性隔热涂层,具有低导热系数、良好的高温相稳定性和断裂韧性等优点。随着动力系统强化程度的不断提高,关键部件常常在极端高温环境下服役,容易导致涂层发生开裂、分层、退化而过早失效。然而,目前关于长寿命热障涂层的失效机制、材料选择及结构设计缺乏相关系统总结。总结几种典型的热障涂层失效机制:残余应力失效、高温烧结失效、钙-镁-铝-硅酸盐(CMAS)渗透腐蚀失效和热生长氧化层(TGO)失效,提出减小涂层内部孔隙率、缩小层间热膨胀系数差、降低表面粗糙度等抑制涂层失效的方法。据此,从顶部涂层的材料选择与结构设计两方面阐述热障涂层的研究进展。从材料选择角度,归纳氧化锆和部分钇稳定氧化锆(YSZ)在长时高温环境下出现的问题,总结近年来的一些先进涂层材料,包括氧化物稳定氧化锆、A2B2O7型氧化物、稀土钽酸盐以及自愈合材料。从结构设计角度,介绍不同涂层结构的制备方法,分别从微观结构、耐腐蚀性、涂层内部热应力、 热循环寿命等方面对层状结构、柱状结构、纳米结构和功能梯度结构进行归纳。综述相关研究现状不仅能指出现有研究的不足及未来研究的发展方向,还能为开发更高抗腐蚀性、更好隔热性和更长寿命的新一代 TBCs 提供理论依据。 |
关键词: 热障涂层 失效机制 陶瓷材料 结构设计 |
DOI:10.11933/j.issn.1007-9289.20231008002 |
分类号:TG156;TB114 |
基金项目:国家自然科学基金(52105232);中央高校基本科研业务费专项(2022YQJD04, 2024ZKPYJD09) |
|
Research Progress on Failure Mechanism, Material Selection and Structural Design of Long-life Thermal Barrier Coatings |
LIU Yuwei1,LI Chun1,FENG Shizhao1,WANG Ye2,ZHOU Shujun1,JIN Shuang3
|
1.School of Mechanical Electronic and Electrical Engineering, China University of Mining andTechnology(Beijing), Beijing 100083 , China ;2.China North Vehicle Research Institute, Beijing 100072 , China ;3.School of Mechanical Engineering, Beijing Institute of Technology, Beijing 100081 , China
|
Abstract: |
Thermal barrier coatings (TBCs) are efficient functional insulation coatings applied to power equipment such as aircraft engines and gas turbines. They have advantages such as low thermal conductivity, good high-temperature phase stability, and fracture toughness. With the continuous enhancement of power systems, key components must often be used in extremely high temperature environments, which can easily lead to the cracking, delamination, degradation, and premature failure of a coating. Therefore, the development of thermal barrier coatings high insulation values and long lives is very important. This article summarizes several typical failure mechanisms of thermal barrier coatings, including failure induced by stress, failure caused by sintering, and failure caused by the infiltration of calcium-magnesium-aluminum silicate (CMAS) and thermally grown oxide (TGO). In order to reduce the residual stress, it is necessary to gradually improve the failure prediction models of TBCs with different preparation processes and different materials, which will improve the reliability and accuracy of the prediction model results. On the other hand, the coating strain tolerance can be increased to release the residual stress, such as by increasing the porosity of the coating and prefabricating cracks in it, which will alleviate the coating stress concentration. In view of the problem of high-temperature sintering, methods to adjust the internal pore structure of the coating by doping metal oxides in the matrix require further study. The thermal-mechanical-chemical coupling effect can be considered to delay the erosion of CMAS, and an in-situ autogenous method can be used to prepare a dense layer, but there have been few studies on this aspect. In addition, a TGO layer with large grain size can be prepared on the surface of the adhesive layer in advance, which can slow down the grain boundary diffusion and limit the growth of TGO by increasing the grain size. Methods have been proposed to reduce the internal porosity of the coating, reduce the difference in interlayer thermal expansion coefficients, and reduce the surface roughness to suppress coating failure. Therefore, the progress on thermal barrier coating research is summarized from two aspects: material selection and the structural design of top coatings. From the perspective of material selection, the problems with using zirconia and some yttrium-stabilized zirconia (YSZ) in long-term high-temperature environments are summarized. In recent years, some advanced coating materials have been developed, including oxide-stabilized zirconia, A2B2O7 oxide, rare-earth tantalite, and self-healing materials. In order to reduce the residual stress, it is necessary to gradually improve the failure prediction models of TBCs with different preparation processes and materials, which will improve the reliability and accuracy of the prediction model results. On the other hand, the coating strain tolerance can be increased to release the residual stress, such as by increasing the porosity of the coating and prefabricating cracks in it, which will alleviate the coating stress concentration. In view of the problem of high-temperature sintering, methods to adjust the internal pore structure of the coating by doping metal oxides in the matrix require further study. The thermal-mechanical-chemical coupling effect can be considered to delay the erosion of CMAS, and an in-situ autogenous method can be used to prepare a dense layer, but there have been few studies on this aspect. In addition, a TGO layer with large grain size can be prepared on the surface of the adhesive layer in advance, which can slow down the grain boundary diffusion and limit the growth of TGO by increasing the grain size. From the perspective of structural design, preparation methods for different coating structures have been introduced. Layered structures, columnar structures, nanostructures, and functionally graded structures are reviewed from the perspectives of their microstructures and corrosion resistance, internal thermal stress, and thermal cycle life values. Finally, the future development directions for long-life thermal barrier coatings are outlined. This review not only discusses the shortcomings of the existing research and direction of future research, but also provides a theoretical basis for the development of a new generation of TBCs with higher corrosion resistances, better thermal insulation values, and longer lives. |
Key words: thermal barrier coating failure mechanism ceramic materials structural design |
|
|
|
|