引用本文: | 刘方圆,魏连峰,张薇薇,郑勇,商乔,王亚峰,张然.等离子体喷涂致密陶瓷涂层技术研究进展[J].中国表面工程,2024,37(5):195~219 |
| LIU Fangyuan,WEI Lianfeng,ZHANG Weiwei,ZHENG Yong,SHANG Qiao,WANG Yafeng,ZHANG Ran.Research Progress in Plasma Spraying Dense Ceramic Coating Technology[J].China Surface Engineering,2024,37(5):195~219 |
|
|
|
本文已被:浏览 745次 下载 390次 |
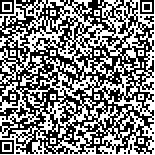 码上扫一扫! |
|
等离子体喷涂致密陶瓷涂层技术研究进展 |
刘方圆1,魏连峰1,张薇薇2,郑勇1,商乔1,王亚峰1,张然1
|
1.中国核动力研究设计院反应堆燃料及材料重点实验室 成都 610213 ;2.四川大学数学学院 成都 610065
|
|
摘要: |
等离子体喷涂陶瓷涂层技术具有加热温度高、沉积速率快、基体受热小、材料范围广和投资成本低等显著优势,广泛应用于航空航天、核能发电和兵器装备等领域。随着现代工业的快速发展,高端装备和部分关键零部件对陶瓷涂层的服役性能提出了更高的使用要求,如何提高等离子体喷涂陶瓷涂层的密度和力学性能成为该领域的研究热点。研究者近年来采用优化的等离子体喷涂技术制备了性能优异的致密陶瓷涂层。系统综述该技术的研究进展,对于其大规模推广应用具有重要意义。 首先,从常规大气等离子体喷涂技术的原理和涂层沉积过程,介绍常规大气等离子体喷涂陶瓷涂层的技术特点、显微特征和瓶颈问题。然后,从等离子体喷枪的结构设计、工作原理和涂层性能,系统综述 8 种用于制备致密陶瓷涂层的等离子体喷枪技术。而后,根据高效能等离子体喷涂工艺的原理、特点和涂层特征,详细阐述超低压、长层流和悬浮溶液 3 种致密陶瓷涂层等离子体喷涂工艺。最后,总结等离子体喷涂致密陶瓷涂层技术的发展现状,并对未来发展趋势进行了展望。主要综述等离子体喷涂致密陶瓷涂层技术的先进喷枪结构和高能效喷涂工艺,可为等离子体喷涂致密陶瓷涂层技术的广泛应用提供借鉴和指导。 |
关键词: 等离子体喷涂 致密陶瓷涂层 等离子体喷枪 等离子体喷涂工艺 |
DOI:10.11933/j.issn.1007-9289.20230920004 |
分类号:TG174 |
基金项目: |
|
Research Progress in Plasma Spraying Dense Ceramic Coating Technology |
LIU Fangyuan1,WEI Lianfeng1,ZHANG Weiwei2,ZHENG Yong1,SHANG Qiao1,WANG Yafeng1,ZHANG Ran1
|
1.Key Laboratory of Reactor Fuel and Materials, Nuclear Power Institute of China, Chengdu 610213 , China ;2.School of Mathematics, Sichuan University, Chengdu 610065 , China
|
Abstract: |
Owing to their high melting point, strength, and hardness, ceramic coatings have been widely used as wear-resistant, corrosion-resistant, and thermal barrier coatings in fields such as aerospace, nuclear power generation, and weapon equipment. Plasma spraying is a highly promising surface cladding technology and has the advantages of a high heating temperature, high deposition rate, low substrate temperature, wide range of spraying materials, and low investment cost, making it one of the most widely used methods for preparing high-performance ceramic coatings. However, with the rapid development of the modern industry, critical equipment or components operating in extreme environments have higher requirements for the service performance of ceramic coatings. Therefore, improving the density and mechanical properties of plasma-sprayed ceramic coatings has become a popular research topic in this field. In recent decades, researchers worldwide have produced various high-performance dense ceramic coatings using optimized plasma spraying technology. Thus, summarizing the current research progress in this technology is highly significant owing to its large-scale promotion and application. First, the technical characteristics, microstructural features, and main issues of conventional atmospheric plasma spraying (APS) ceramic coatings are introduced from the aspects of the working principle and coating deposition process. Owing to the rapid energy dissipation and severe arc fluctuations associated with conventional APS technology, typical atmospheric plasma-sprayed ceramic coatings contain a large number of unmelted or semi-melted powder particles, as well as rich defect structures, such as large-scale pores and interlaminar cracks. This makes it difficult for the performance of ceramic coatings deposited by the conventional APS process to meet the requirements of industrial applications that require coatings with low porosity and mechanical properties, such as wear-resistant coatings, electrolytes of solid oxide fuel cells, and environmental barrier coatings. Subsequently, the structural design, working principle, and coating performance of eight plasma torch technologies for preparing dense ceramic coatings are systematically reviewed. By optimizing the electrode structure, powder feeding method, plasma jet protection, and heating method of the plasma torch, the operational stability, plasma jet energy output, powder heating, and acceleration efficiency of the plasma torch can be effectively improved. This is beneficial for preparing dense ceramic coatings with low porosity and excellent mechanical properties. Subsequently, the principles, process characteristics, and coating features of three typical high-efficiency plasma spraying processes for preparing dense ceramic coatings are elaborated in detail. By improving the operating pressure, plasma jet length, and powder injection method of the plasma spraying process, three dense ceramic coating plasma spraying processes, namely, very-low-pressure plasma spraying, long laminar plasma spraying, and suspension or solution precursor plasma spraying, are developed. These technologies effectively enhance the energy input and utilization efficiency of the plasma spraying process, significantly improving the heating and acceleration performance of refractory ceramic particles in the plasma jet, and are successfully applied in the preparation of various types of high-performance dense ceramic coatings. Finally, the development status of plasma-sprayed dense ceramic coating technology is summarized, and future development trends are discussed. This paper systematically summarizes the plasma torch technology and plasma spraying process used for preparing dense ceramic coatings, and is expected to provide a reference and guidance for the widespread application of plasma-sprayed dense ceramic coating technology. |
Key words: plasma spraying dense ceramic coating plasma torch plasma spraying process |
|
|
|
|