引用本文: | 黄东保,周霆伟,郁海涛,贾玺泉,徐震霖,何宜柱,董振启,张慧勇.结晶器铜板表面HVOF喷涂NiCrCoBSi多主元合金涂层的高温磨损性能[J].中国表面工程,2024,37(5):275~287 |
| HUANG Dongbao,ZHOU Tingwei,YU Haitao,JIA Xiquan,XU Zhenlin,HE Yizhu,DONG Zhenqi,ZHANG Huiyong.High-temperature Wear Performance of NiCrCoBSi Multiple Principal Elements Alloy Coating Sprayed by HVOF on the Surface of Crystallizer Copper Plate[J].China Surface Engineering,2024,37(5):275~287 |
|
|
|
本文已被:浏览 522次 下载 380次 |
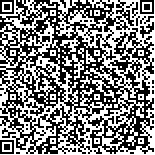 码上扫一扫! |
|
结晶器铜板表面HVOF喷涂NiCrCoBSi多主元合金涂层的高温磨损性能 |
黄东保1,2,周霆伟1,郁海涛1,贾玺泉1,徐震霖1,何宜柱1,董振启2,张慧勇1
|
1.安徽工业大学材料科学与工程学院 马鞍山 243002 ;2.泰尔(安徽)工业科技服务有限公司 马鞍山 243002
|
|
摘要: |
针对连铸结晶器铜板在服役过程中的磨损失效问题,采用超音速火焰喷涂(HVOF)技术在结晶器铜板表面制备了 NiCrCoBSi 自熔性多主元合金涂层,以提高铜板的耐磨性能。利用 XRD、SEM、TEM 等方法研究了 NiCrCoBSi 涂层的微观结构;借助摩擦磨损设备对其耐磨性进行评价,并与市场化占有率最高的电镀 NiCo 涂层进行对比。结果表明:NiCo 涂层为单相面心立方(FCC)固溶体结构,而 NiCrCoBSi 涂层的主要物相包括 FCC 固溶体、CrB 和 M23C6。与 NiCo 涂层相比,NiCrCoBSi 涂层的硬度提高了 95%,而断裂韧性只下降了 5.4%。磨损测试后发现两种涂层的磨损机制均以黏着磨损、疲劳磨损为主,伴随着少量磨料磨损。NiCrCoBSi 涂层表现出优异的耐磨性和较低的摩擦因数,其磨损率较 NiCo 涂层降低了 81%。NiCrCoBSi 涂层耐磨性较高的主要原因是其较高的硬度、内部的各种硬质耐磨相以及磨损表层的加工硬化。这是因为在循环载荷作用下, 涂层产生塑性变形,涂层的硬质相在塑性变形过程中被切割、旋转,导致碳化物及硼化物被细化和球化,从而提升了磨损表层的硬度。制备了具有优异高温耐磨性能的 NiCrCoBSi 自熔性多主元合金涂层,为长寿命铜及其合金涂层的开发提供了理论依据和技术参考。 |
关键词: 超音速火焰喷涂 多主元合金 铜板 涂层 磨损 |
DOI:10.11933/j.issn.1007-9289.20230626001 |
分类号:TG142 |
基金项目:安徽省重点研究与开发项目(2022a05020017);国家自然科学基金(51271001) |
|
High-temperature Wear Performance of NiCrCoBSi Multiple Principal Elements Alloy Coating Sprayed by HVOF on the Surface of Crystallizer Copper Plate |
HUANG Dongbao1,2,ZHOU Tingwei1,YU Haitao1,JIA Xiquan1,XU Zhenlin1,HE Yizhu1,DONG Zhenqi2,ZHANG Huiyong1
|
1.School of Materials Science and Engineering, Anhui University of Technology,Ma'anshan 243002 , China ;2.Taier (Anhui) Industrial Technology Service Limited Company, Ma’anshan 243002 , China
|
Abstract: |
Crystallizers are the core components of continuous casting equipment, and their quality directly impacts billet quality and production efficiency. With the advancement of high-drawing-speed continuous casting technology, higher performance requirements for crystallizers have been proposed, particularly concerning wear, a major cause of crystallizer copper plate failure. Currently, electroplated crystallizer coatings hold approximately 80% of the market share. However, the long deposition cycle, low hardness, tendency for coating peeling, and environmental pollution caused by electroplating technology make it inevitable for this technology to be phased out. Supersonic flame spraying (HVOF) is one of the most widely used thermal spraying technologies, capable of producing highly dense and uniform coatings due to its fast flame flow rate, high powder kinetic energy, and low oxidation levels. In addition, the HVOF technology offers a wide range of material options and can be functionally designed to accommodate different sizes and parts of the crystallizer, meeting continuous casting requirements. A NiCrCoBSi multiple principal element alloy coating has been applied to the surface of crystallizer copper plates using HVOF technology to improve their high-temperature wear performance of copper plates. The microstructure of the NiCrCoBSi coating was studied using X-ray diffraction, scanning electron microscopy, and transmission electron microscopy. The wear resistance of the coatings was evaluated using frictional wear equipment and compared with that of the commonly marketed electroplated NiCo coating. Additionally, the wear mechanisms of the coatings were analyzed. The results showed that the NiCo coating had a single-phase face-centered cubic solid solution structure, whereas the NiCrCoBSi coating exhibited an FCC solid solution, with CrB and M23C6 as the main phases. Both coatings had high densities with no observed cracks. A clear delamination was found between the NiCo coating and the copper alloy substrate, with no transition zone, indicating a mechanical bond. In contrast, a diffusion layer between the NiCrCoBSi coating and the copper alloy substrate due to diffusion heat treatment after spraying, resulting in the formation of a metallurgical bond. Compared to NiCo coating, NiCrCoBSi coating exhibited a 95% increase in hardness, whereas the fracture toughness decreased by only 5.4%. The friction factor of the NiCo coating fluctuated significantly, ranging from 0.4 to 1.0, and eventually stabilizing around 0.6. Compared with the NiCo coating (0.67), the friction factor of NiCrCoBSi coating is lower (0.51), with the curve showing good stability, ranging from 0.4 to 0.6, and ultimately stabilizing at around 0.52. After wear, the surface of the NiCo coating exhibited large flakes accompanied by dark gray adhesive marks, cracks, and debris. The worn surface of the NiCrCoBSi coating showed signs of debris, peeling, furrowing, and adhesive wear, with many small peeling pits. The wear mechanisms of both coatings were adhesive and fatigue wear, accompanied by a small amount of abrasive wear. The wear rate of NiCrCoBSi coating was 1.53×10?5 mm·N?1 ·m?1 , which is about five times higher than that of NiCo coating (7.91×10?5 mm·N?1 ·m?1 ). The main reasons for the higher wear resistance of the NiCrCoBSi coating are the better hardness, various wear-resistant phases, and the work hardening of the wear surface layer. This hardening occurs due to the plastic deformation of the coating under cyclic loading, during which the hard phases of the coating were cut and rotated. The carbides and borides are refined and spheroidized, enhancing the hardness of the wear surface layer. This research paves the way for developing coatings with excellent wear resistance for copper and their alloys. |
Key words: high-velocity oxygen fuel multiple principal elements alloys copper plate coating wear |
|
|
|
|